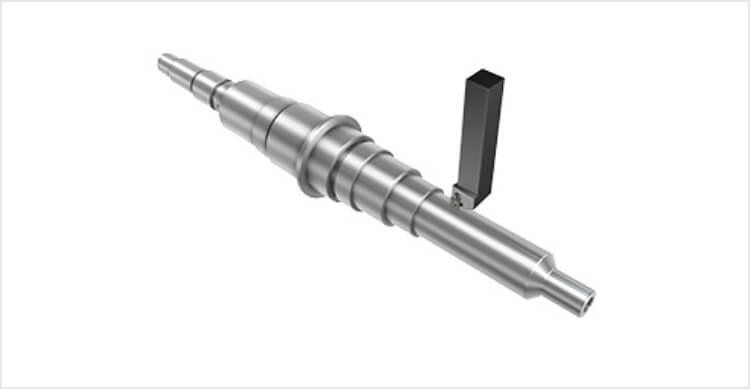
Turning
Turning generates cylindrical and rounded forms with a single point tool. The turning definition is that the tool is stationary with the workpiece rotating. A turning operation is the most common process for metal cutting and is a highly optimized process, requiring thorough consideration of the various factors in the turning application. Turning can be broken down into a number of basic applications (longitudinal turning, facing and profiling), requiring specific type of tools, cutting data and programming for the operation to be performed in the most efficient way.
In parting and grooving, process security and productivity are two important aspects. With the correct set up and choice of tools there are many difficulties that can be avoided when parting off. Difficulties such as pips and burrs, tool breakage, chip jamming, poor surface finish on components with complex grooves, incorrect coolant pressure, long overhangs and high levels of vibration, which ultimately may cause expensive components to be scrapped. To help you avoid these specific difficulties and successfully perform parting and grooving, we have provided the following recommendations and tips.
General Turning-ISO
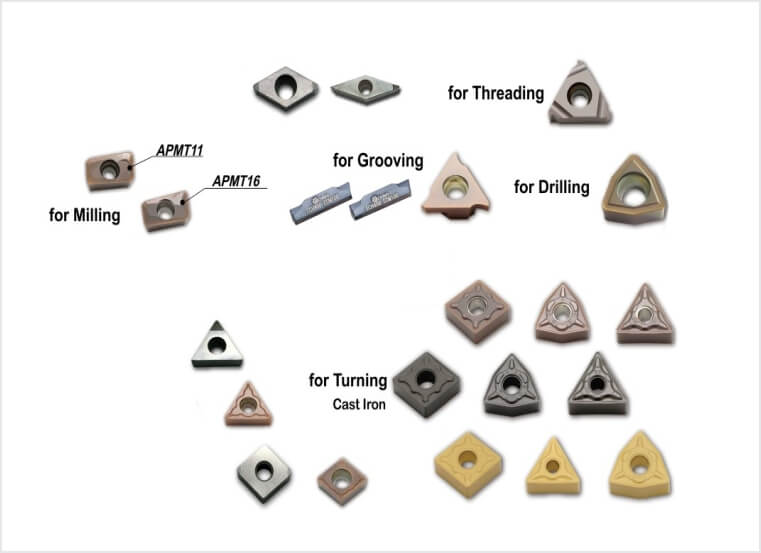
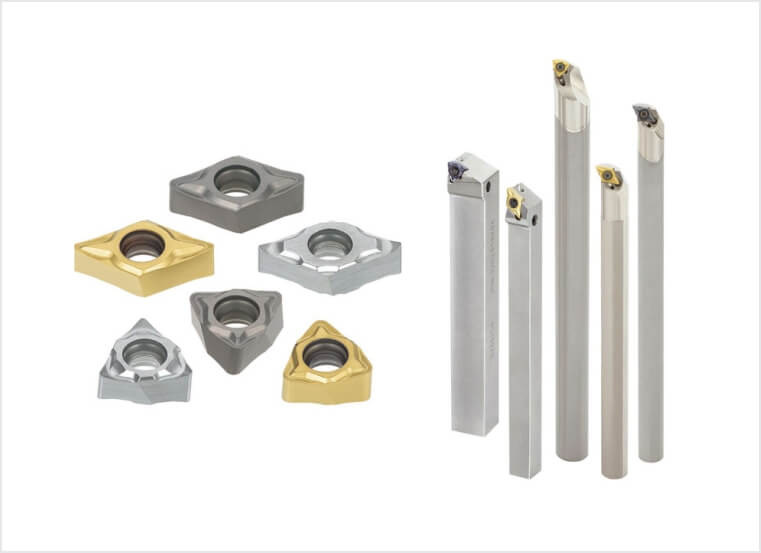
Grooving and Parting-Off
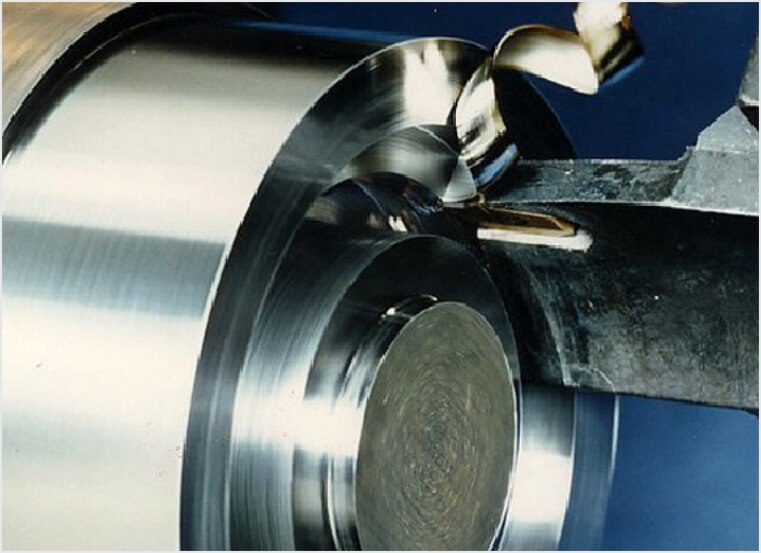
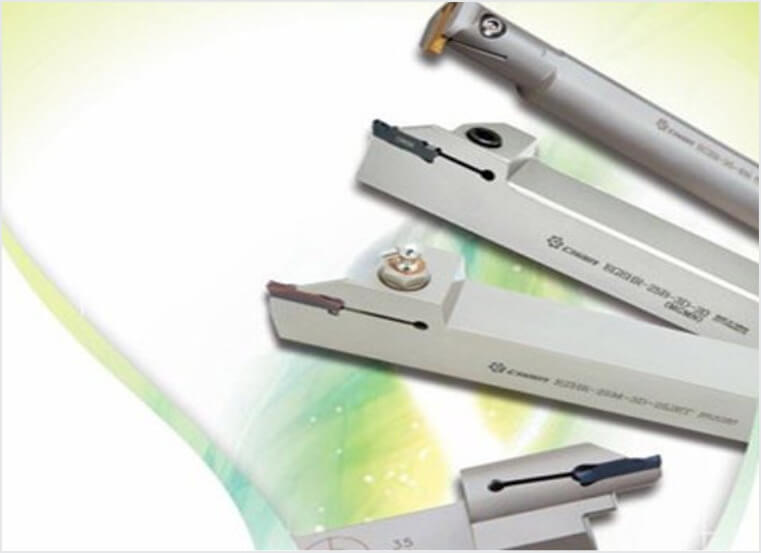
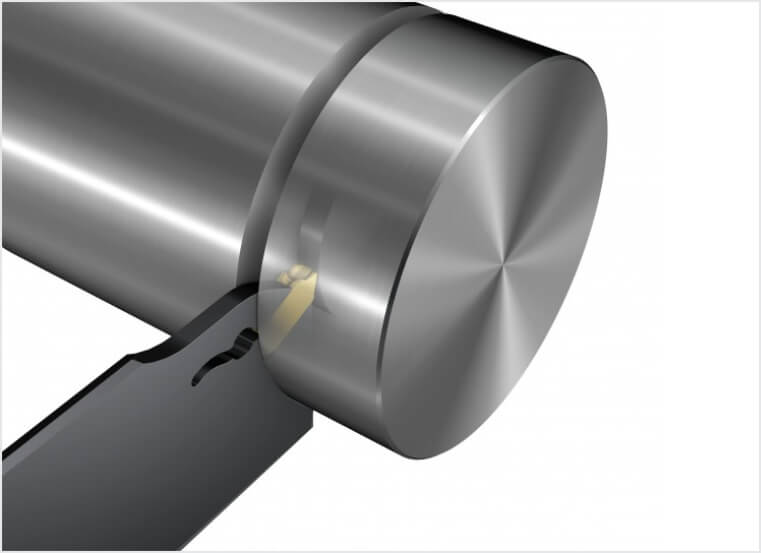
Advance Cutting Materials (CBN,PCD)
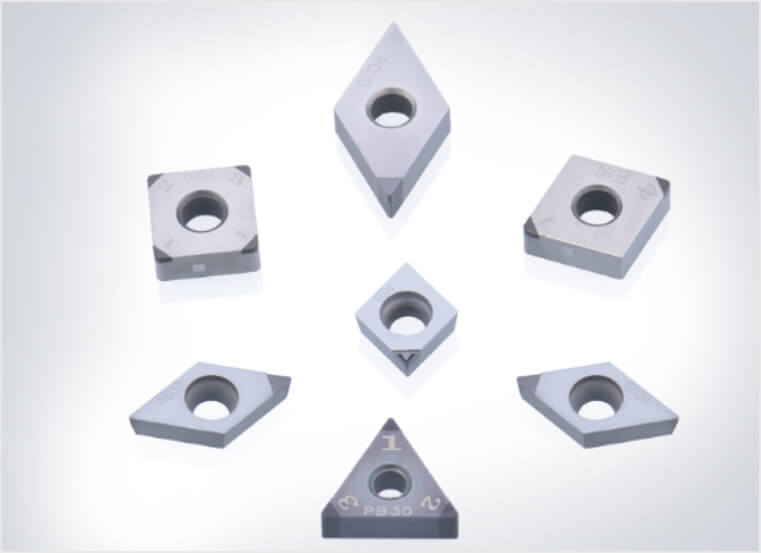
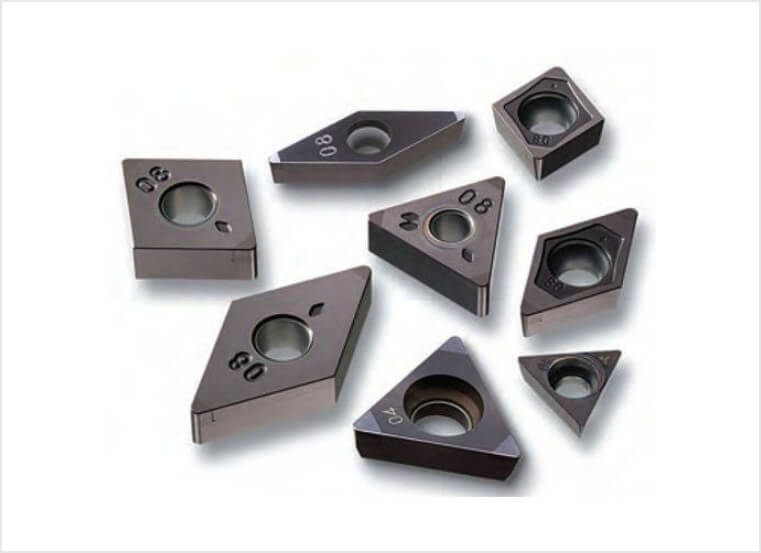